The commonly used linear shaft transmission methods for laser cutting machines include ball screws, gear racks, and linear motors.
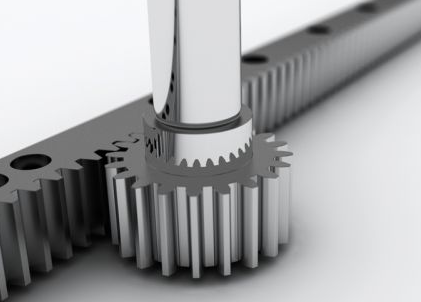
Rack is a special gear distributed on a strip, divided into straight rack and helical rack, which are used in pairs with straight cylindrical gear and helical cylindrical gear, respectively. Gear and rack transmission is widely used, which can achieve high speed and large stroke.
Which is better for a rack and pinion drive, a straight rack or a helical rack?
The answer is: The advantages of helical rack are mainly reflected in the following aspects:
1. Good meshing performance: When a straight cylindrical gear meshes, its contact line is a straight line parallel to the axis. When the tooth profile simultaneously enters or exits meshing along the tooth width, it is prone to cause impact and noise, and the transmission stability is poor, making it unsuitable for high-speed gear transmission. The contact line of helical gear teeth is a straight line inclined to the gear axis. When engaging helical cylindrical gears, due to certain limitations in tooth height, the length of the contact line gradually increases from zero during the meshing of two tooth profiles, and gradually decreases from a certain position until it disengages. That is, both the entry and disengagement of helical gears are gradual, resulting in stable transmission and low noise, At the same time, this meshing method also reduces the impact of manufacturing errors on the transmission.
2.Large coincidence ratio: it can reduce the load on each pair of teeth, thereby improving the bearing capacity of the gear, ensuring smooth transmission, and extending the service life of the gear.
3.The minimum number of teeth that a helical standard gear does not produce undercut is less than a spur gear, so using helical gear transmission can achieve a more compact structure.