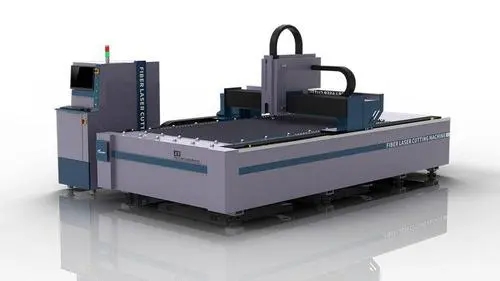
1. Laser tube outlet
The laser tube is the most important component that has the greatest impact on the cutting effect. It determines all operations, such as machining effectiveness, cutting performance, etc. If this situation occurs, the main measuring component should be the laser tube, which should be replaced for damage. If there is no damage, it should be cleaned.
Damaged focusing lens
Excessive cutting speed, damage to the focusing lens, poor focusing effect, incorrect optical path, and unstable voltage are all reasons for the opacity of laser cutting
3. Laser beam path
The optical path of the laser beam will determine the intensity of laser irradiation. If the laser beam weakens during the optical transmission process, the processing board is likely to continue cutting. At this point, it should be checked whether the optical path is in the center and whether it passes through the center. If the laser does not pass through the hole, it is easy to generate diffraction phenomenon, which will weaken the power and beam of the laser tube. It can be solved by increasing the working current.
4. Laser tube deformation
The laser tube is the main factor determining the laser. If deformed, cutting faults can also occur. For its treatment plan, the laser tube should be rotated multiple times, and then the optimal support angle should be rotated for treatment, and it should not be replaced due to deformation.
Of course, there are also many factors that lead to unsmooth or opaque cuts in the board, such as problems with the material itself, insufficient auxiliary gas pressure, and poor cooling system water turbidity and heat dissipation effect. Taking the issue of opacity in laser cutting seriously and finding solutions to these problems is of great significance for improving production efficiency and ensuring the quality of laser cutting.
Reasons for the inability of fiber laser cutting machine to cut workpieces
1. Auxiliary gas
As is well known, when using fiber laser cutting machines for cutting, a certain amount of auxiliary gas is required. At this point, the auxiliary gas must have sufficient pressure to completely remove the waste generated by cutting. Generally speaking, when cutting thicker workpieces, the air pressure should be reduced, as the residue adhering to the workpiece can damage the cutting edge. Increasing the air pressure can increase the cutting speed, but after reaching the maximum value, continuing to increase the air pressure will cause a decrease in the cutting speed. This interference can affect the melting efficiency, sometimes changing the mode structure and reducing the cutting quality. If the beam is too divergent, causing the spot to be too large, and even causing serious consequences of ineffective cutting.
2. Accuracy of the workbench
If the accuracy of the workbench is uneven or for other reasons, it can also lead to high-precision laser cutting effects.
3. Laser beam
The beam emitted by the laser is conical, so the cutting gap is also conical. In this case, 0.4mm thick stainless steel is much smaller than 3mm. Therefore, the shape of the laser beam is the main factor affecting the cutting accuracy of metal laser cutting machines. The thicker the workpiece, the lower the accuracy, so the larger the cutting seam. Even for the same material, if the composition of the material is different, the cutting accuracy will also vary. Therefore, the material of the workpiece also has a certain impact on the accuracy of laser cutting.